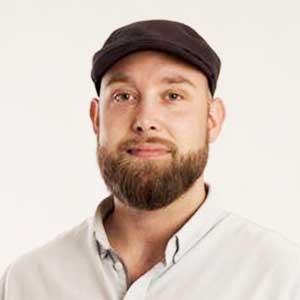
Jesper Veber Jeppesen
Specialist in 3D laser modelling and CEO at Bygkontrol
3D laser scanning saves project managers time and money as it depicts a full 3D view of the scanned project.
Based on precision equipment and put together in a pointcloud, 3D laser scanning takes measurements and pre-registration to the next level.
3D laser scanning is a time-saving procedure that minimizes errors compared to traditional measurements which are prone to human error and inconsistency. Not only is 3D scanning useful for as-built constructions, to compare to a 3D BIM model of the project, it also has a relevant place in the renovation of old buildings.
In fact, it is when refurbishing existing buildings, particularly period properties, that the new laser technology comes into its own. Anyone on a construction site will have seen basic point-to-point laser measurement devices that give accurate measurements. They may seem smart, but they are nowhere as sophisticated as the latest 3D laser scanning technology.
Digital twins
The latest 3D laser scanning technology creates a digital universe of the existing project, meaning a 3D scanning of the project as its digital twin. Using technical 3D survey equipment project managers can record and document the existing conditions on the project.
3D laser scanning is the fastest way to measure and map a building inside, as well as exterior. This way it is possible to measure wall and beam thickness, window and facade areas on existing buildings. It is similarly possible to compare an as-built project during the construction, to detect and avoid errors.
Life–like models
The technology is particularly proving useful in renovating older buildings because it can be used to provide an accurate model of the property as it is now, not how it was when plans were last drawn up.
Jesper Veber Jeppesen is a specialist in 3D laser modelling and CEO at Bygkontrol. He points out that many of the projects he works on need accurate readings in the present day to feed into BIM software because so much has changed in the past decades, or even the last century or so.
“Because refurbishments projects often are old buildings which has been subject to many changes over time, the architects find that the original drawings or the most recent drawings are not accurate as they are not showing everything on the existing building,” he says.
“It means they often end up working off plans that don’t closely resemble what the building looks like because new windows or doors or beams have been put in. So, in the pre-registration stage, they need to get an accurate model of the building to see what they are actually working on. Otherwise it’s not possible to seriously work with the project.”
Saving time and money
Traditionally, getting a building accurately measured could take highly trained engineers or architects many weeks and, even then, the process is subject to human error. By using 3D laser modelling, Jeppesen claims there are substantial gains, because the technology is directly linked to the computer. Measuring and recording up to 5000 m2 per day with a 3D laser scanner, this exceeds the project size a human can measure and record by an ordinary disto measurer.
“It can cost about a third as much to use 3D laser scanning compared to having a couple of guys with tape measure or laser pointers do the work manually,” he says.
“The problem with manual measurement is it relies on the accuracy of the user and when each measurement needs to be manually written down and typed into a computer, there is a lot of scope for errors to creep in.”
Far more accurate than single laser measurement
Rather than take a single reading at a time, which needs to be noted down, 3D laser scanning operators can scan a large room to a far greater degree of accuracy than a single laser measuring device. Every reading is instantly fed into a computer device and put together as a giant point cloud. From this point cloud it can be built into a highly accurate 3D model.
“I recently got asked to go out to a massive five story building which had taken a couple of guys more than a month to measure and there were too many mistakes for the architects to move forward with complete confidence. It took me a week to get a highly accurate set of readings fed straight into the computer from which I could then build a 3D model,” Jeppesen says.
Laser 3D modelling is also proving invaluable in new buildings by allowing a construction manager to compare the work completed on a project so far, compared to the original model drawn up on BIM software.